Resin 3D Printing
Service
Fast Delivery
UK wide
Quick turnaround
high quality resin 3D printing service
Resin 3D
Printing Details
3D print your models with high-precision SLA 3D printing. SLA, or Stereolithography, utilizes lasers to cure liquid resin layer-by-layer, creating incredibly detailed prototypes, intricate designs, and even functional end-use parts. Our wax resin enables clients to produce metal castings from the 3d printed part itself. Our clear resin is fantastic choice for anything that requires transparency, its almost class like with clear glossed and doesnt yellow like many other clear resins.
- MAX PRINT SIZE : 156mm x 278mm x 295mm
- MATERIAL : Rigid Engineering Resin, Castable Wax
- COLORS : White, Black, Grey & Clear
- LAYER HEIGHT : 0.07mm layer height
- PRODUCTION LEAD TIME : 1 or 3 working days
- MINIMUM ORDER : £30
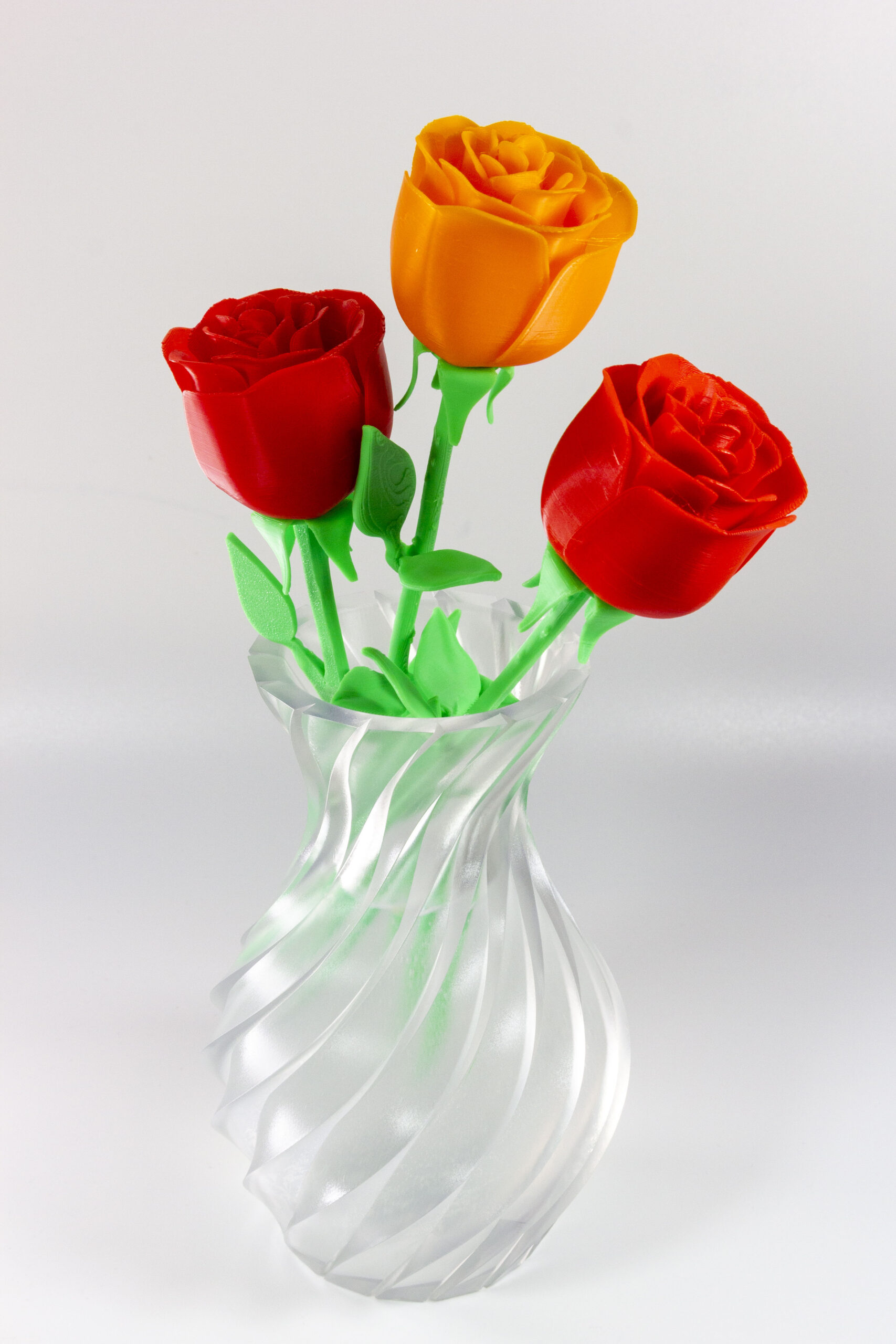
- What you need to know about our resin 3D Printing service
We offer an SLA resin 3D printing service in north London. SLA printing is capable of building extremely fine detailing. Most FDM and SLS 3D printers print at 0.1mm layer heights, our SLA printers print as low as 0.07mm.
The surface finish is the smoothest of all 3D printing technologies, it most closely mimics injection moulded products therefore it’s the closest thing to the finished product. It’s ideal for producing silicone moulds largely because the surface is smooth. Our resin doesn’t inhibit the curing of most tin and platinum-based casting silicones so its suitable for most moulding applications.
Microworkshops SLA resin 3D printing service, can offer quick turnaround times of 1 or 3 working days.
Colours To Choose From
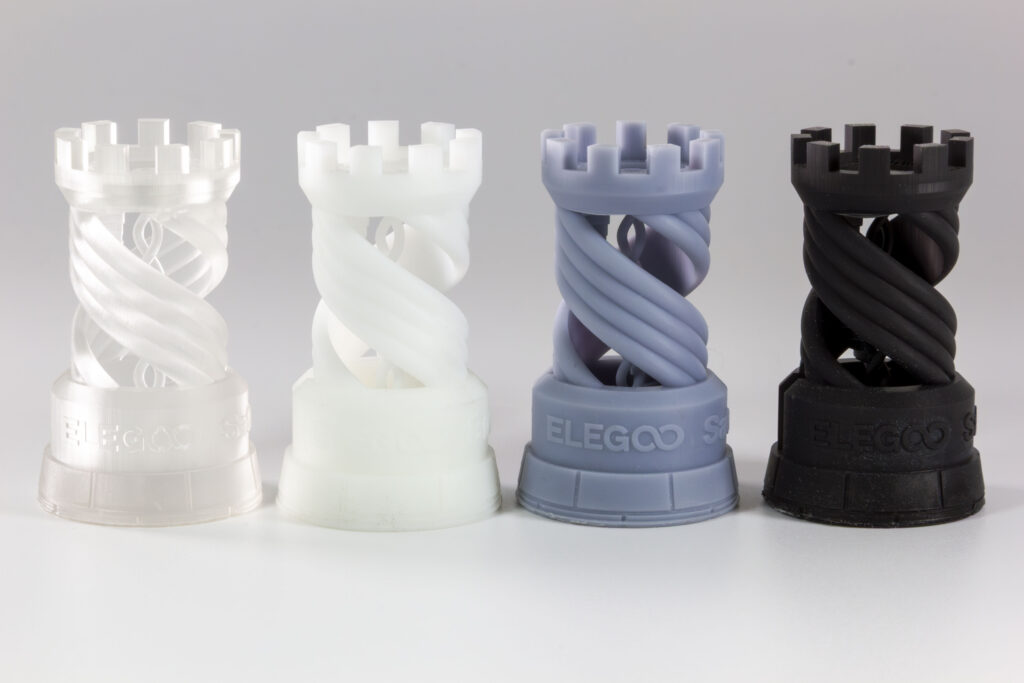
SLA Colors

- What is Stereolithography
First patented in 1986, by Chuck Hall. Sterelithography machines use an ultra-violet light. They build models by changing liquid resin solid, as well as, photopolymerization. This process is repeated layer by layer until the solid model is complete. This forms each layer. Furthermore, highly intricate detail, can be achieved in a short space of time. There are two types of SLA printers: bottom-up and top-down. In our case we use DLP/MSLA 3D printers which are not technically the same as SLA printer, but for all intent and purposes they are the same. MSLA/DLP printers use a LCD screen to project the 405nm lights rather than UV lasers used by SLA machines.
Post Processing
SLA 3d printing requires the highest level of post processing. unlike other printing technologies the material starts as a viscous liquid which is cured by UV light into its solid form. When prints are finished supports must be removed, it must be washed in 100% IPA solution, further curing required to move the print from 'green state' to its final hardened form.
RESIN MATERIAL PROPERTIES
01
Viscosity: 250-550 MPa*s
02
Absorption band: 385nm-410nm(wavelength)
03
Desity: 1.05-1.13 g/cm3
05
Flexural Modulus: 966 MPa
06
Thermal Deformation Temperature HDT: 70 degrees C
07
Volume Shrinkage: 0.2-0.7%
08
Tensile Strength: 39.13 MPa
09
Tensile Modulus: 497 MPa
10
Shore Hardness: 85D
Rigid resin
Overview
Rigid resin is a strong engineering plastic that is formed with UV light. Its raw state before printing is in liquid form as with all light based 3d printing resins. It has properties that we have found are suited well for a range of difficult geometries including forms prone to warping.
It has a remarkably low shrink rate of 0.2-0.7% which is how we produce forms within tolerance and free of warping. Its scores well in tensile strength so its strong and rigid. Its elongation percentage prevents it from becoming brittle and provides a little flexibility. Its highly machinable meaning all secondary operations like planar sanding, drilling, milling and tapping can be performed with greater ease. Parts under 100 grams are usually printed solid, for parts over 100 grams we will hollow the object for you, this is necessary to prevent printing failures.
We normally apply a wall thickness of 3mm giving it more than adequate strength. Typically, this resin is best suited to applications where fine detail and surface quality is most important. If you want a 3d print that most closely represent a real injection moulded consumer product then this is the material for you.
- Printing Technology : SLA Resin
- MAX PRINT SIZE : 156mm x 278mm x 295mm
- MATERIAL : Rigid Engineering Resin, Castable Wax
- COLORS : White & Grey
- LAYER HEIGHT : 0.07mm layer height
- PRODUCTION LEAD TIME : 1 or 3 working days
- MINIMUM ORDER : £30
Properties
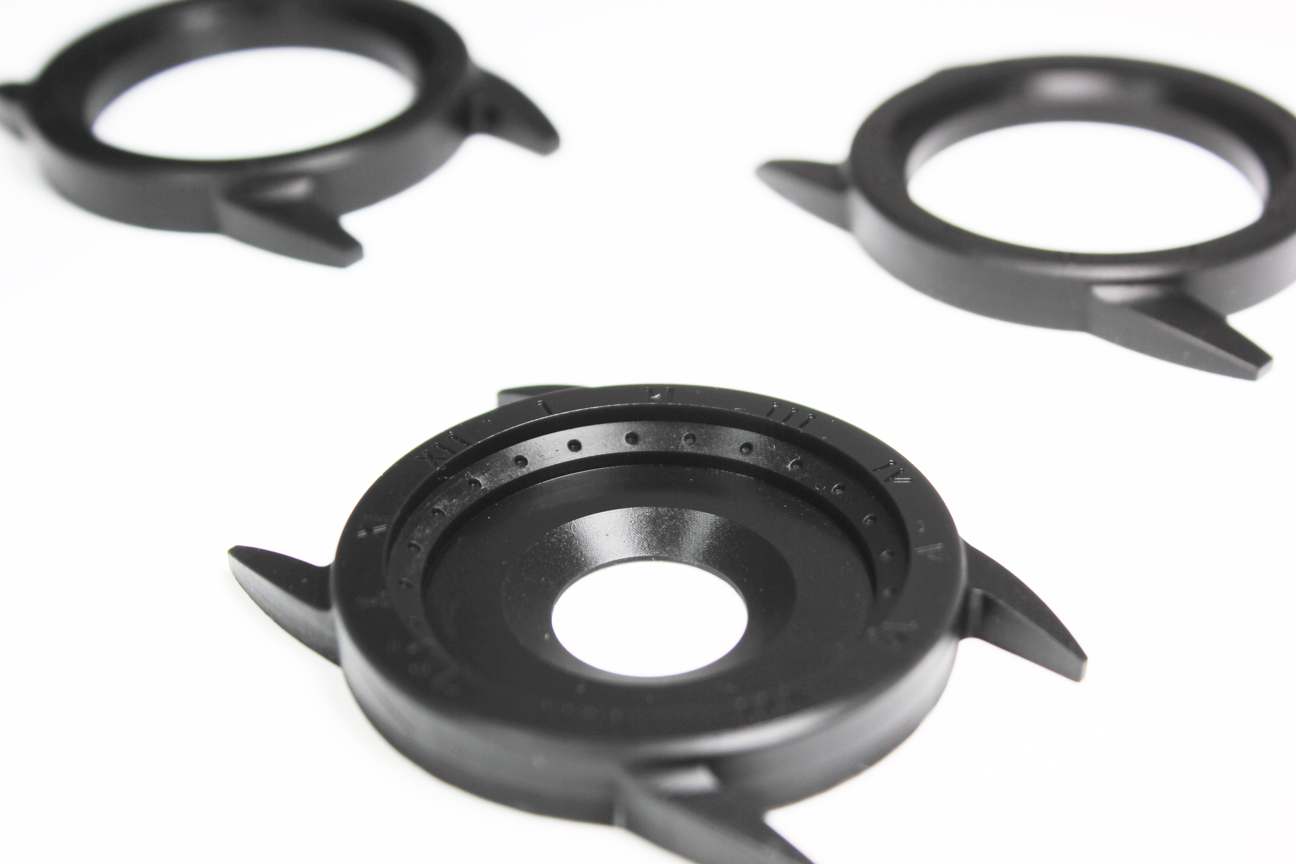
Dimensionally Accurate
It has a particularly low shrink rate (0.2-0.7%) ideal for functional parts that require high dimensional accuracy. Most standard resins on the market have a shrink rate of 2% and up.
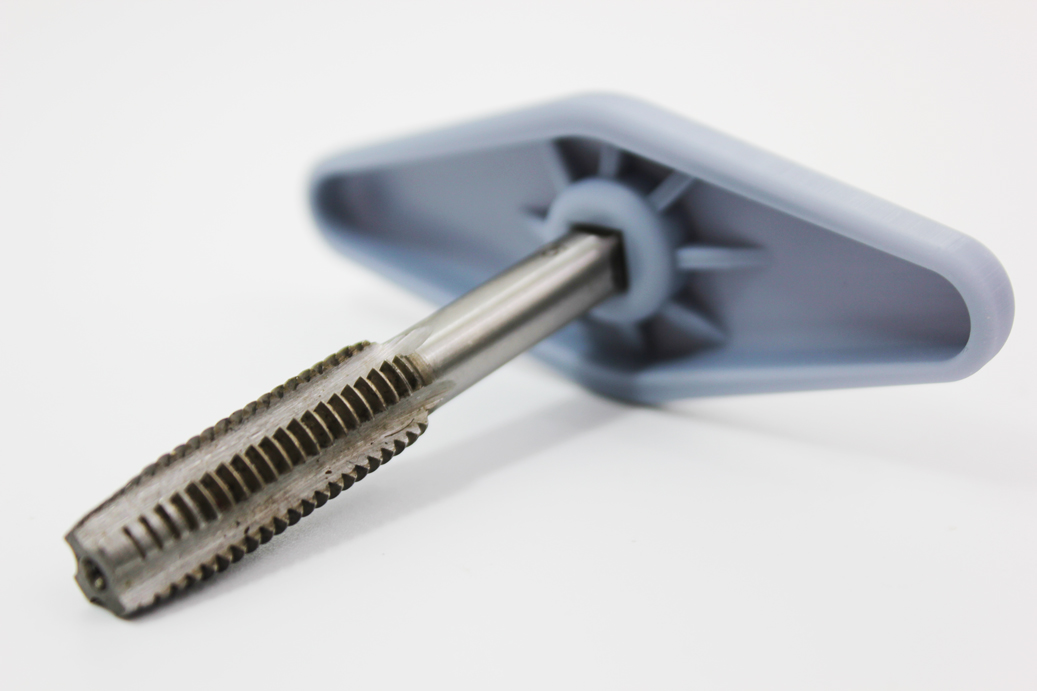
Tough & Rigid
Its strong and impact resistant like ABS. It has a shore 85D hardness making it stiff. Although it is stiff especially in thick areas it is still touch enough to withstand some bending.
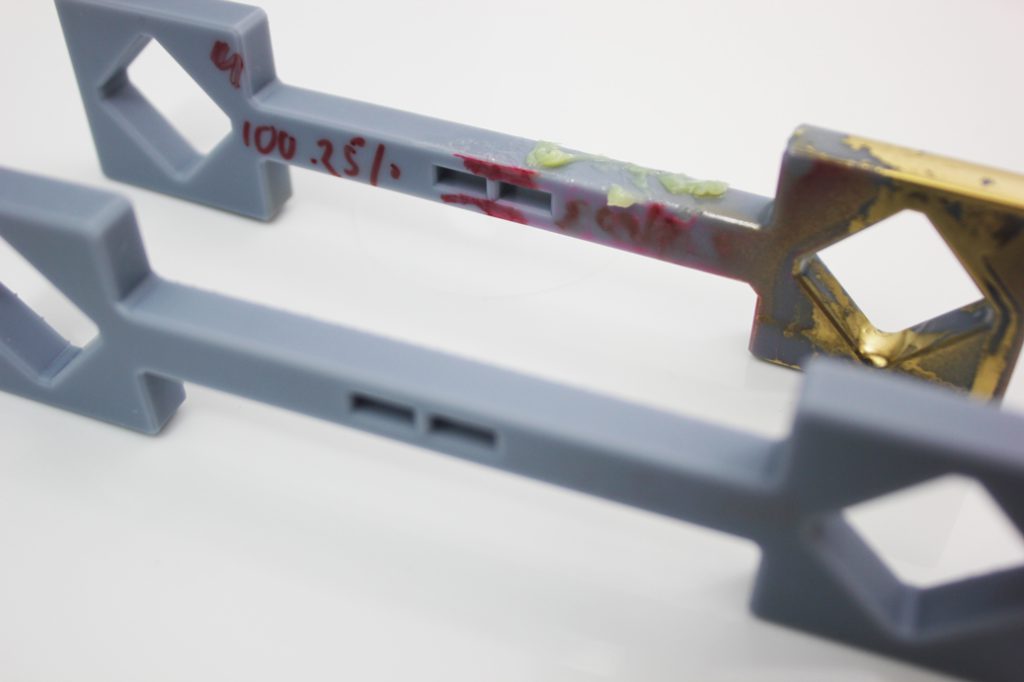
Chemically Resistant
It offers good chemical resistance, its non-reactive with paint, oil, machine greases, water, glue, spirits and silicone. Nearly all paints adhere well to the surface, it can be glossed and it works perfectly for silicone moulding applications.
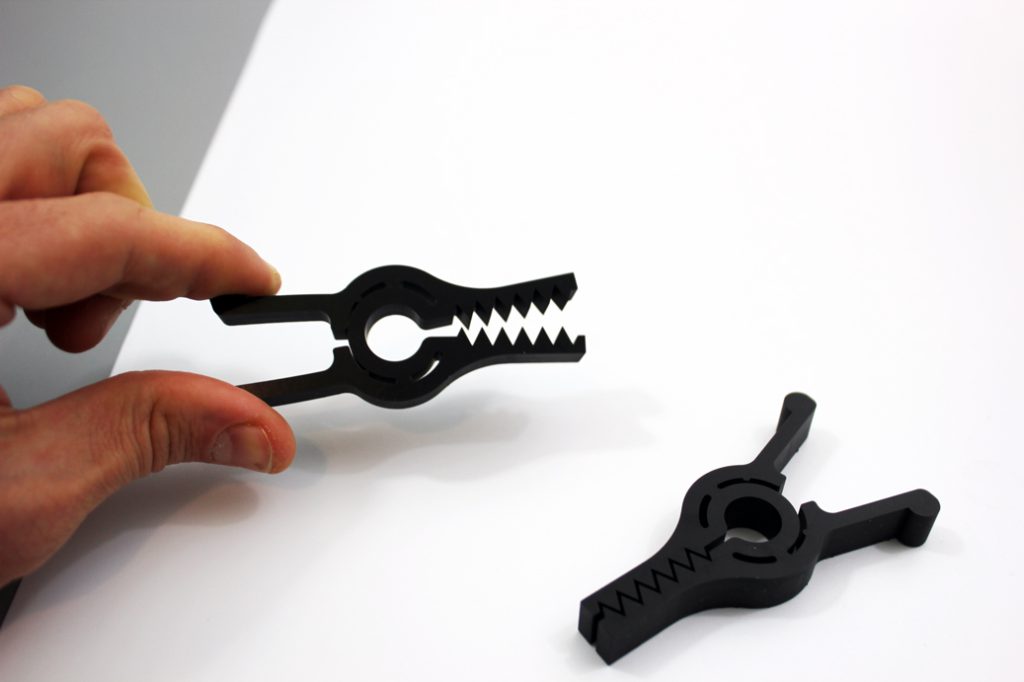
Slightly Flexible
Non-brittle with a little flexible (having a 37% elongation at break). Just enough give to improve impact strength and resist permanent deformation
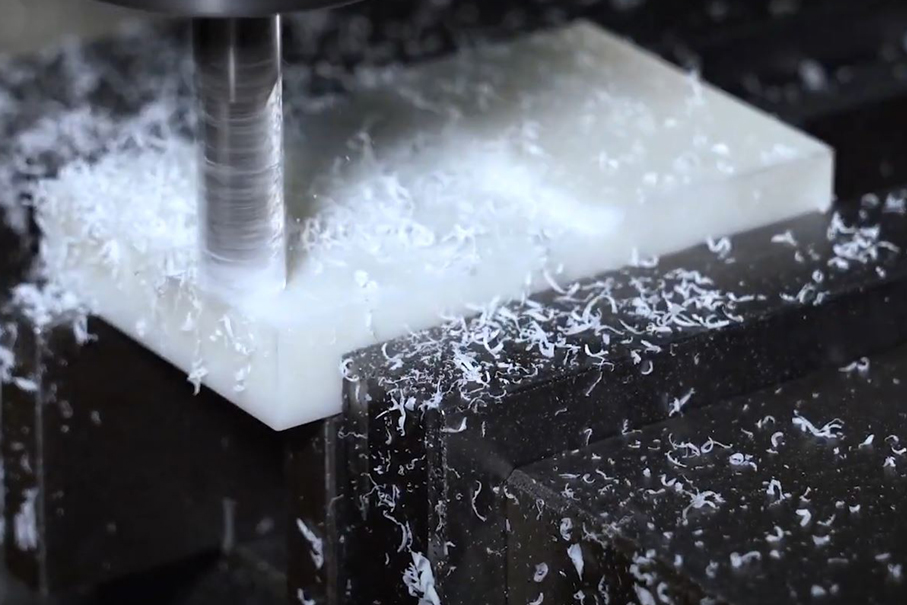
Easily Machinable
It’s very easily machined, you can drill holes, tap threads, mill or turn with CNC and lathe. This is handy when for example you model a hole location incorrectly, instead of reprinting you can drill the hole where it needs to be. If the hole is too tight, you can redrill with a larger bore.
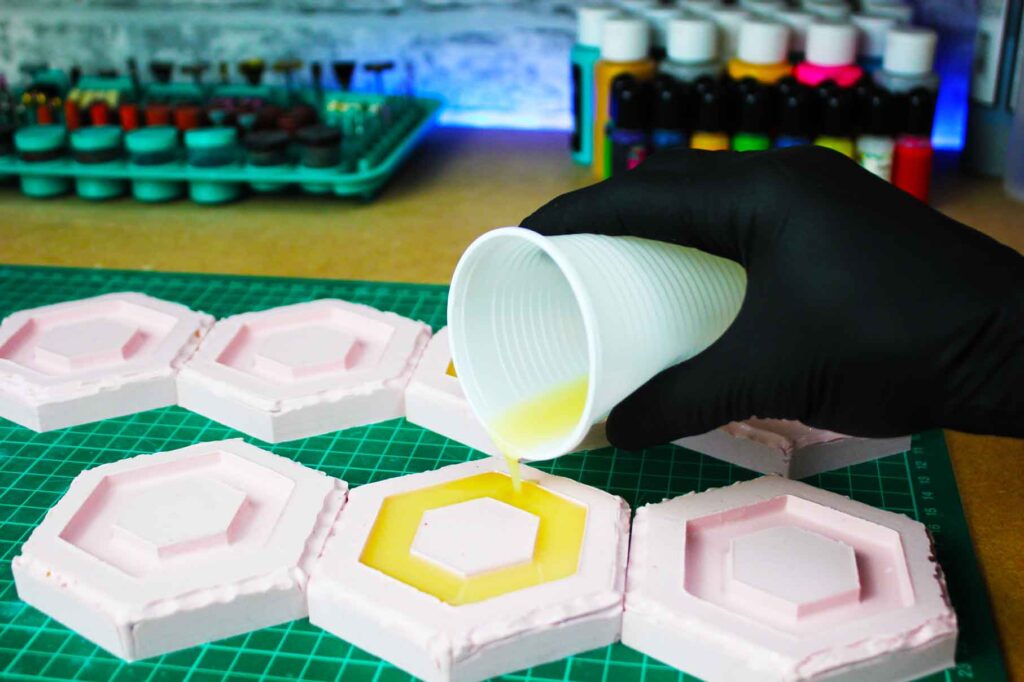
Silicone moldable
Rigid Resin is always the first choice with silicone moulding. This rigid resin is detailed and smooth and doesn’t inhibit the curing of most tin-based and many platinum based silicones.
Tolerance/Accuracy
The vast majority of our prints are with +-0.2mm (or +-0.2%). We offer a guaranteed tolerance of +-0.3mm (or 0.3%), however 95% of our parts are significantly more precise than the minimum tolerance we offer.
If the part is less that 100mm long, then it will be within 0.1mm of its target size.
In rare cases some geometries are prone to warping which can lead to results outside of the guaranteed tolerance, if this is the case, we can usually reorientate the print direction to compensate. This resin also has a very low shrink rate which we’ve found mitigates warping more than any other resin we use or have tested.
Mechanical Properties | Test Method | Value |
---|---|---|
Ultimate Tensile Strength | ASTM D638 | 39.13 MPa |
Tensile Modulus | ASTM D638 | 497 MPa |
Elongation at Break
| ASTM D638 | 35.66% |
Yield Point Elongation
| ASTM D638 | 5.94% |
Flexural Strength | ASTM D790 | 46.6 MPa |
Flexural Modulus
| ASTM D790 | 966 MPa |
Notched IZOD
| ASTM D256 | 364.2 J/m |
Shrinkage | / | 0.2-0.7% |
Shore Hardness | ASTM D2240 | 85 D |
Viscosity | ASTM D445 | 250-550 MPa*s |
Density | ASTM D792 | 1.05-1.13 g/cm3 |
Range of wavelengths | / | 385-410 nm |
HDT @0.45MPa
| ASTM D648-18 | 70 degrees C |
Look/Feel/Finish
Below you will see pictures of the Rigid Resin fresh out of the printer before and after its post processing stage. There are various finishing methods you can apply to the surface including wet sanding, painting or glossing. By default, we remove the supports and sand away the marks (included in the price), however sometimes surfaces within pockets or odd crevices are not accessible enough to be sanded (in a time/cost efficient manner), so will be left unsanded.
The surface is naturally smooth but a light sanding then ideally a wet sand buffs away even the smallest of blemishes leaving it looking just like a commercially moulded part. To do this yourself all you need is high grit sandpaper (200+ grit). If the part has many fine details wet sanding may not be an option (it would buff out the detailing). The smooth surface is partially due to its layer height (only 0.05mm which as thinner than paper). At the bottom image you can see how the surface compares to our cheaper FDM printing which prints at 0.2mm layer height by default. It’s worth noting that layer thickness isn’t the only factor effecting surface finish, the type of printing technology also plays a significant role.
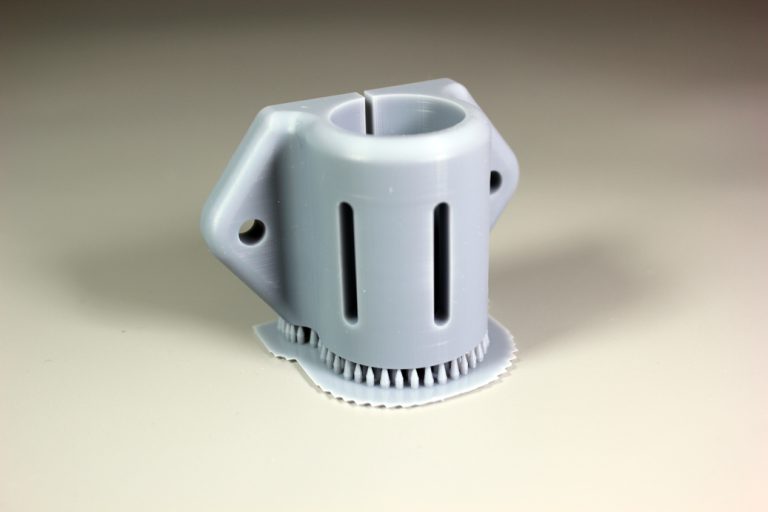
1 - (Above) supports and raft still attached (post processing stage)
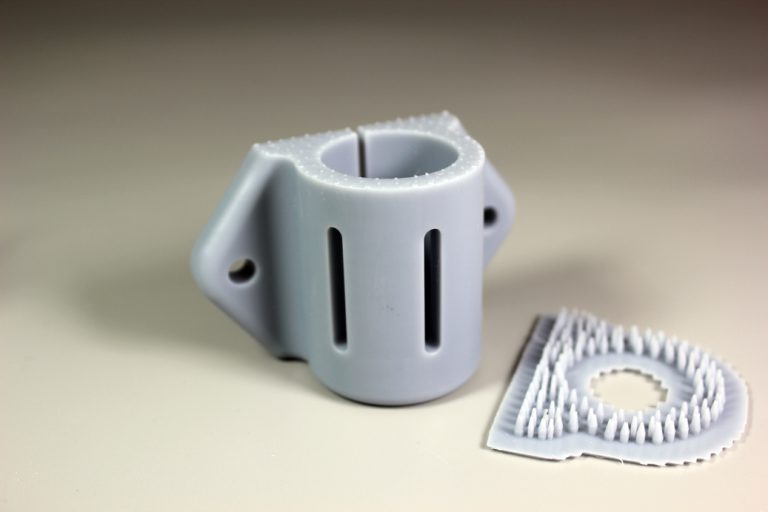
2 - (Above) supports and raft removed (post processing stage)

3 - (Above) close up of the support marks (post processing stage)

4 - (Above) close up of freshly sanded surface (we do for all prints as standard)
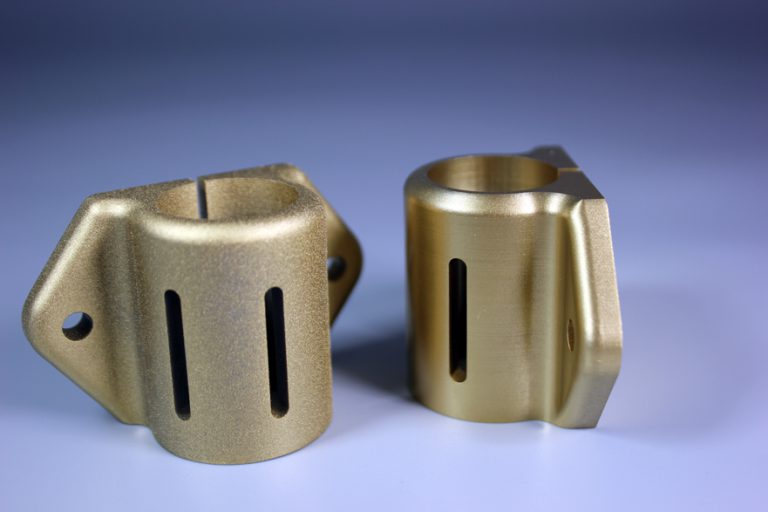
5 - (Above) spray painted for smooth and sandblasted effect
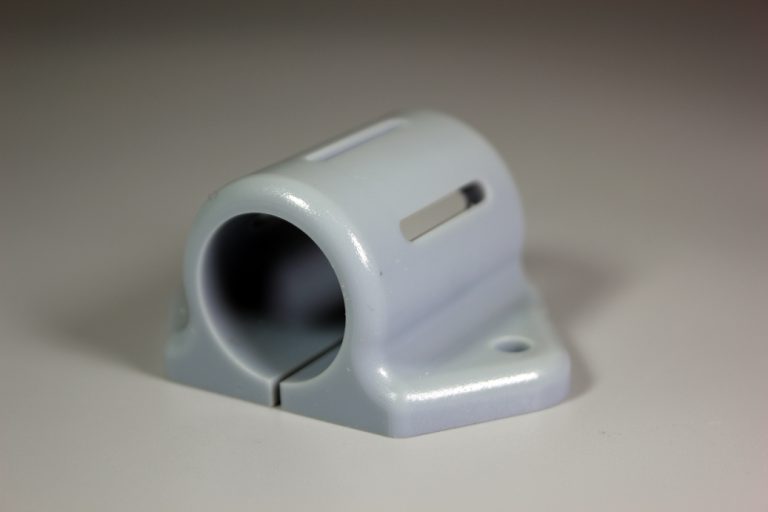
6 - (Above) Glossed - normal clear acrylic gloss from spraycan
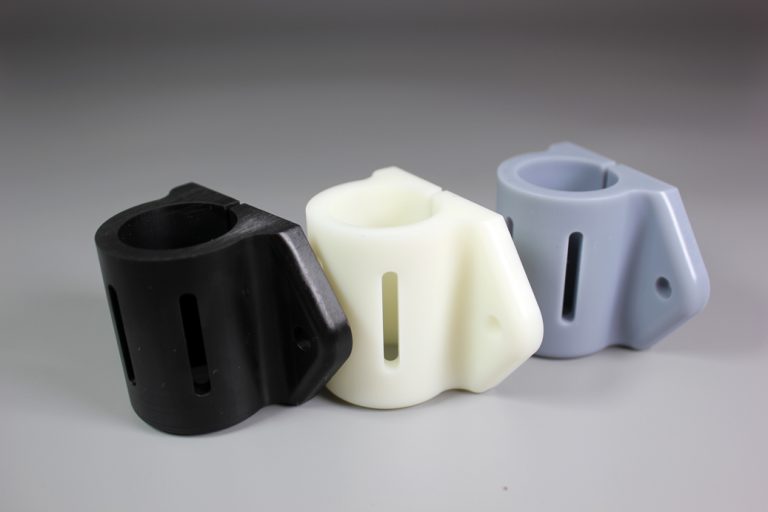